Choosing the Best Defoamers for Your Manufacturing Line
Choosing the Best Defoamers for Your Manufacturing Line
Blog Article
How Defoamers Improve Effectiveness in Production and Production
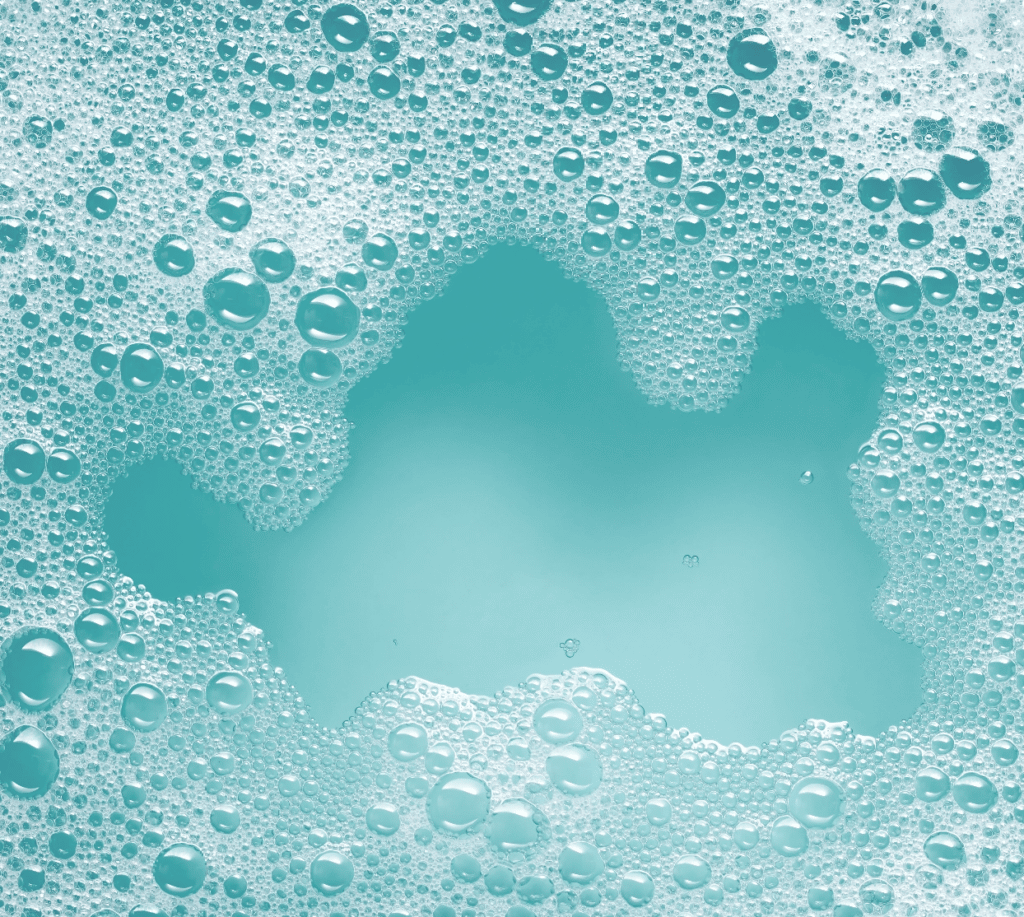
Comprehending Defoamers
Defoamers play an important role in different producing processes by effectively combating the development of foam, which can affect and interrupt operations item quality. Foam can arise in countless contexts, such as during blending, heating, or chemical reactions, potentially resulting in inefficiencies and incongruities in items. The device whereby defoamers run commonly entails lowering the surface area tension of the liquid, enabling bubbles to increase and coalesce to the surface quicker, where they can after that break.
Reliable defoamers not just decrease foam development but also preserve compatibility with the product, ensuring that there are no negative effects on the last outcome. Recognizing the properties and functions of defoamers is vital for suppliers intending to enhance their processes, boost efficiency, and maintain the stability of their items (defoamers).
Trick Benefits of Defoamers
Using defoamers in making procedures offers a variety of considerable benefits that improve operational performance and product high quality. Among the primary benefits is the decrease of foam formation throughout manufacturing, which can block equipment and interfere with process. By decreasing foam, defoamers ensure smoother operations, resulting in lowered downtime and maintenance costs.
In addition, defoamers enhance item uniformity by avoiding air entrapment, which can compromise the integrity of the last item. This is particularly vital in sectors where aesthetic look and texture are critical, such as in paints, layers, and food items. Improved item quality not only satisfies client assumptions but additionally enhances brand name track record.
Additionally, defoamers can help in optimizing source usage. By enhancing the performance of raw product usage, they add to cost financial savings and lowered waste, aligning with sustainability objectives. Finally, the application of defoamers can cause shorter handling times, allowing manufacturers to increase production capability without significant capital financial investment - defoamers.
Applications in Different Industries
In producing processes throughout different industries, the application of defoamers plays a critical duty in enhancing performance and item quality. These chemical ingredients are used in fields such as food and beverage, pharmaceuticals, and textiles to minimize foam-related challenges.
In the food and beverage industry, defoamers are essential during the fermentation process, stopping lathering that can interrupt manufacturing and spoil the product's integrity. Likewise, in the pharmaceutical market, defoamers are utilized in the formula of fluid medications, ensuring uniformity and stability while reducing waste.
Textile manufacturing also takes advantage of defoamers, as they are used in coloring and completing procedures to promote also circulation of dyes and chemicals. This application not just boosts the final product's look however likewise lowers the amount of water and energy eaten during manufacturing.
Additionally, in the paper and pulp market, defoamers aid maintain procedure performance by decreasing foam that can hinder equipment performance. Generally, the diverse applications of defoamers throughout these markets underscore their importance in maximizing production processes and delivering high-quality products.
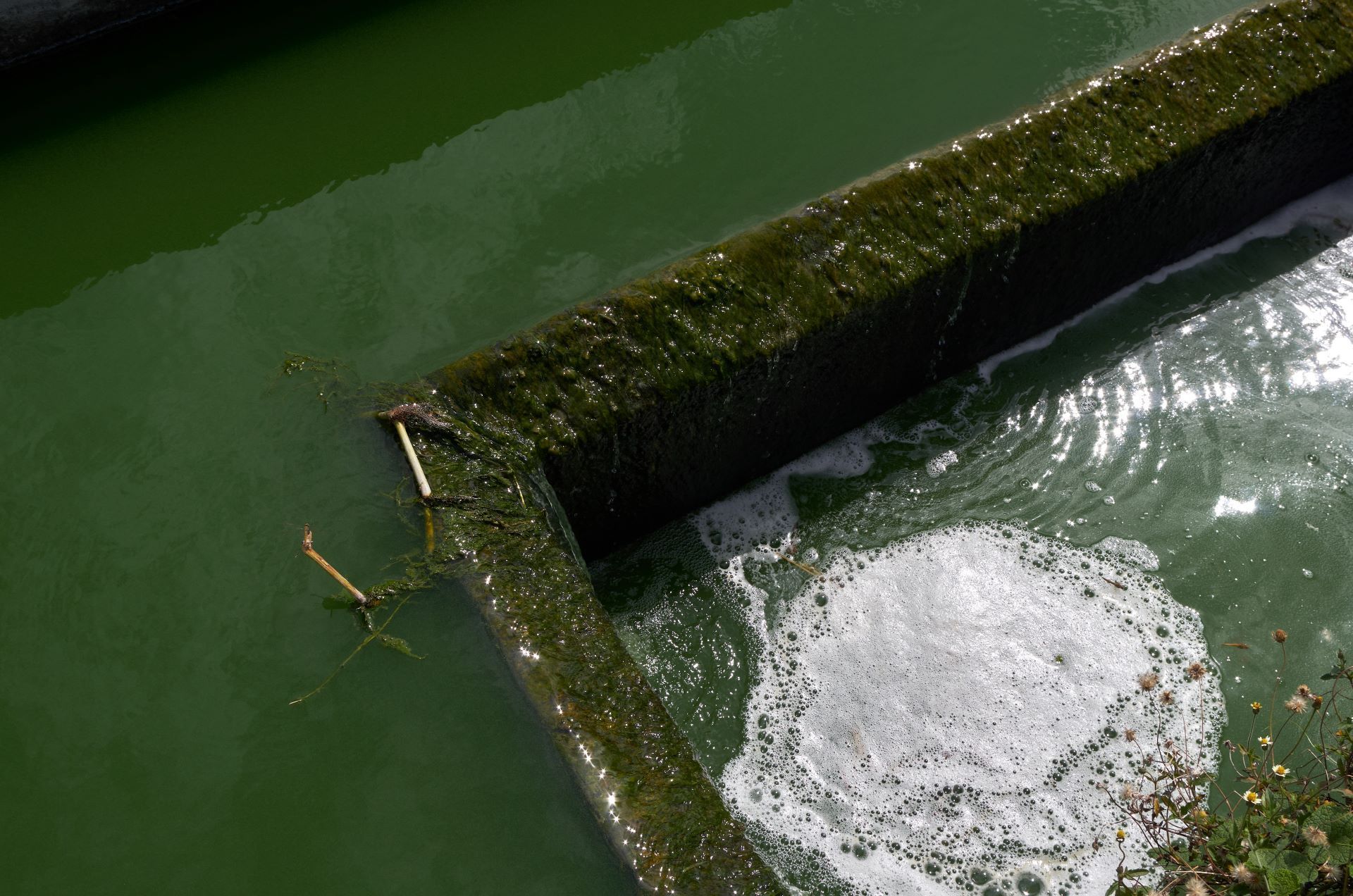
Selecting the Right Defoamer
Choosing an ideal defoamer is important for taking full advantage of performance and top quality in manufacturing procedures. The option of defoamer depends upon different elements, consisting of the specific application, the kind of foam being created, and the formula of the product being made.
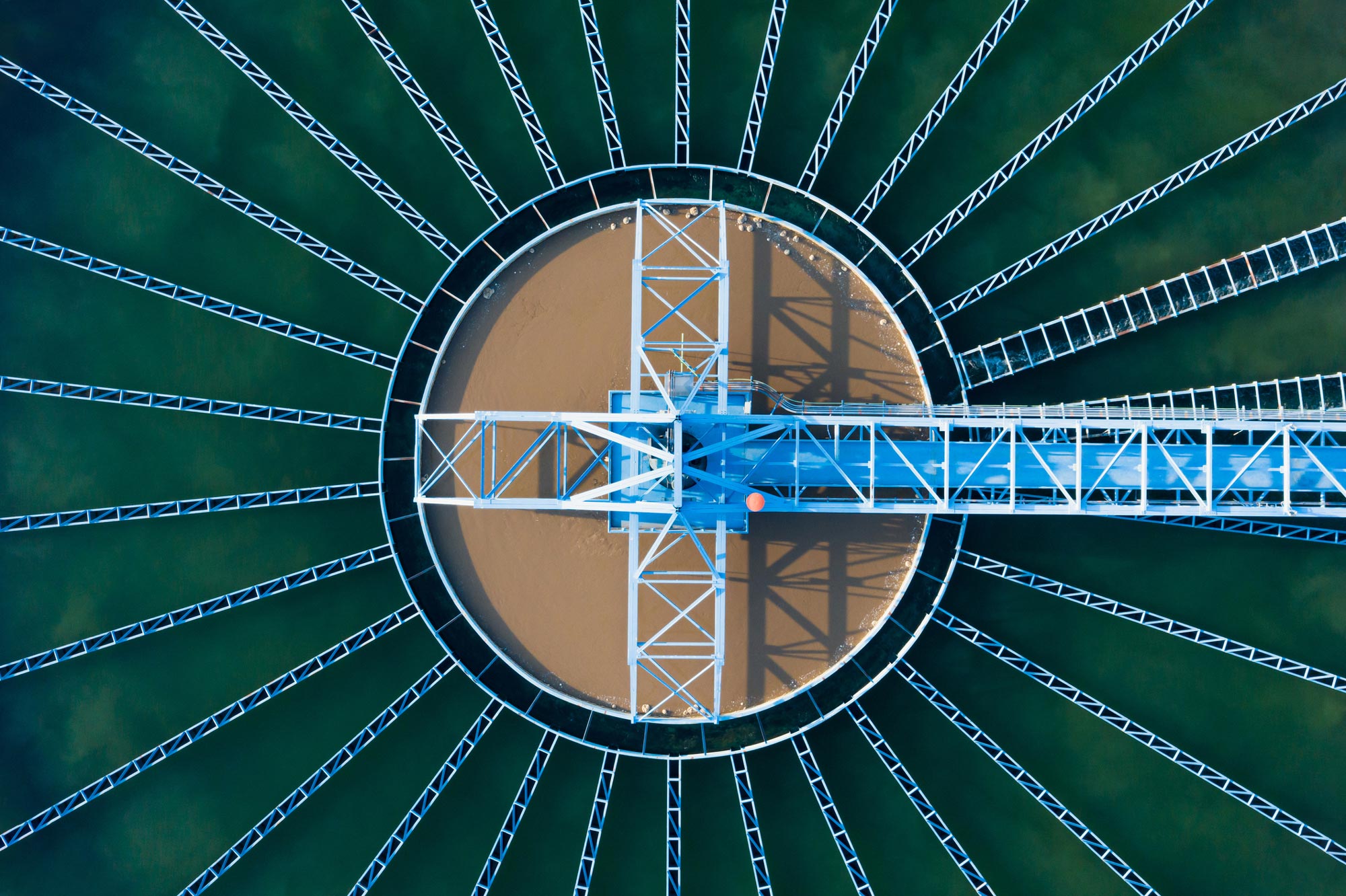
Firstly, think about the chemical compatibility of the defoamer with other ingredients in your formulation. A defoamer that interacts negatively with useful site other elements can adversely influence product quality. Furthermore, the temperature and pH range throughout handling are important; some defoamers execute ideally under specific problems while coming to be inadequate in others.
Secondly, review the defoamer's efficiency characteristics, such as its capacity to rapidly minimize foam and its determination during manufacturing. It is important to select an item that not only removes foam swiftly but additionally preserves its effectiveness gradually.
Lastly, take into consideration regulative and ecological elements, specifically if your manufacturing procedure undergoes strict conformity criteria. Choosing a low-toxicity or biodegradable defoamer can help satisfy sustainability goals while ensuring operational efficiency. By attentively assessing these criteria, makers can make educated choices that boost performance and product stability.
Ideal Practices for Application
Successful implementation of defoamers in making procedures calls for cautious preparation and adherence to best techniques. Picking the right defoamer, as formerly reviewed, is important; ensure it is suitable with the materials included and attends to the determined foaming problems properly.
Following, keep clear interaction with all stakeholders, including drivers and quality assurance teams. Training sessions can help guarantee that everyone understands the application treatments, possible impacts on product quality, and safety considerations. Implementing a test phase can also be useful; monitor performance carefully to evaluate effectiveness and make required adjustments.
In addition, normal screening and monitoring of foam degrees can give beneficial understandings into the defoamer's efficiency in time. Readjusting does in action to changes in production variables will certainly aid keep ideal efficiency - defoamers. Finally, documenting all procedures and results promotes continuous renovation, enabling fine-tuning of defoamer use and improving general performance in manufacturing operations.
Final Thought
In summary, defoamers play an important role browse around this site in boosting efficiency within production and manufacturing processes. By reducing foam development and facilitating bubble coalescence, defoamers contribute to enhanced item high quality, consistency, and functional effectiveness.
The advantages extend to product top quality and expense financial savings, as defoamers help enhance processes.Defoamers play an essential role in different making processes by successfully combating the formation of foam, which can interrupt operations and influence item top quality. Understanding the residential properties and functions of defoamers is vital for manufacturers intending to optimize their processes, boost performance, and keep the stability of their items.
Using defoamers in manufacturing procedures offers an array of substantial advantages you can try these out that enhance functional effectiveness and product high quality.Furthermore, defoamers enhance item uniformity by preventing air entrapment, which can compromise the integrity of the final item.
Report this page